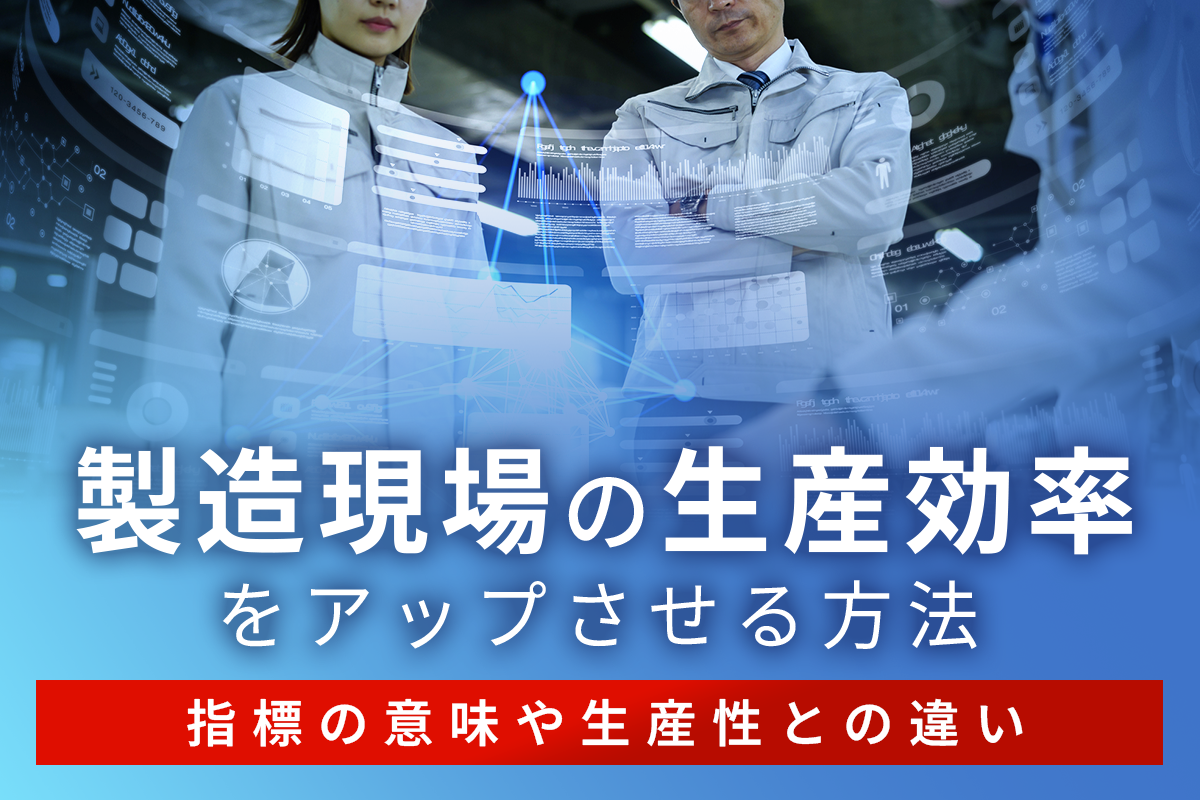
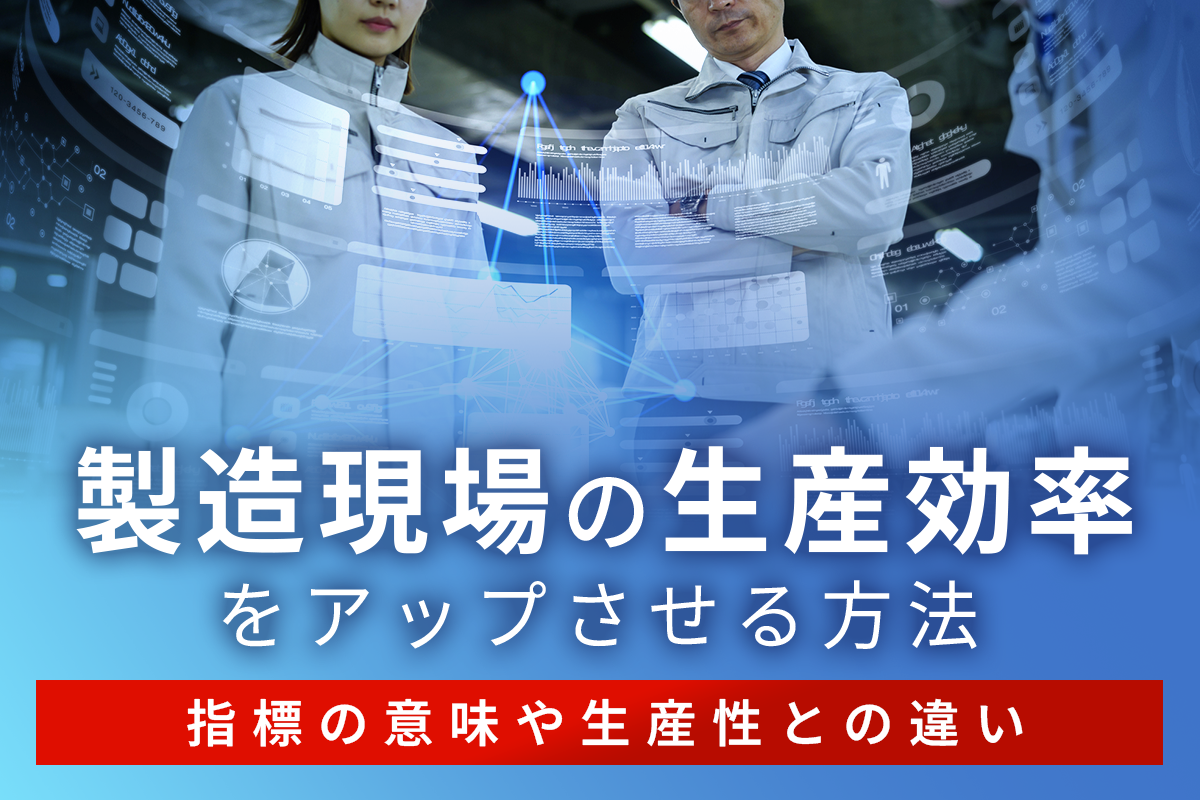
人的ミス・ヒューマンエラーに起因するポカミスは、製造現場における悩みの種のひとつであり、完全な対策を講じるのは難しいものです。そこであらためて考えてみたいのが、製造ラインにおけるポカヨケの仕組み化です。
ポカヨケはトヨタ生産方式にも採用され、多くのメーカーも取り組んでいるポカミス対策の一環です。本記事では、ポカミスが起こる原因を細分化して考察し、7つの具体的なポカヨケの仕組みづくりを取り上げていきます。
お役立ち資料はこちら
ポカヨケとは、製造ラインなどで発生する人間の作業ミス(ポカミス)に起因する、不良品や欠品の発生や想定外の事故などを防ぐための仕組み、あるいは装置のことです。「フールプルーフ」とも言い換えられます。
なお、ポカヨケ・ポカミスの「ポカ」は将棋や囲碁などでは「悪手」の意味で用いられているほか、手落ち、うっかりミスといった意味もあります。「ヨケ」は文字通り、回避するという意味に由来します。
作業マニュアルを整備したり、教育体制を充実させたりしても、ヒューマンエラーを完全になくすことはほぼ不可能です。そのため、人がミスをしにくい状況を構築すべく、製造ラインには以下のようなポカヨケが導入されています。
ポカヨケは、もともとトヨタ生産方式による改善活動(カイゼン)で生まれた言葉です。
トヨタ生産方式では、「ニンベンのついた自“働”化」の概念のもと、機械に異常が生じたときには自動で停止させ不良品の発生を防ぐシステムを取り入れ、人が機械の監視を担う必要性を排除し、生産性の向上を図っています。
ポカヨケも、この「自働化」施策の一環です。現在のトヨタの製造ラインにおいても、単純ミスを防ぐために、組み付け工具と連動して部品の締め忘れの有無を自動的にチェックするシステムなどを導入しています。また、問題が発生したときにはランプでアラートし、不良品の発生を防止しています。
こうした取り組みであるポカヨケは、現在では「poka-yoke」として世界基準の概念として浸透しています。
不良品・欠品の発生の防止や製造ラインのダウンタイム短縮化など、ポカヨケの実施は製造業にさまざまなメリットを還元します。主に次の目的やメリットを背景に、多くの企業にて具体的なポカヨケ対策が導入されています。
ポカヨケの導入によって不良品の発生を防止できると、作業の中断や製造ラインのダウンタイムを短縮化できます。また、不良品が減ることで歩留まり率がアップする結果、生産性の向上にも役立ちます。
ポカヨケの導入は、作業量を増加させることなく品質の向上を図れる点にも大きなメリットがあります。
通常、不良品の発生を減らすために全数検査を実施する場合には、検査工程での作業量が増大化します。検査に時間を要すると納品までのリードタイムも長期化することから、製品の競争力も毀損されるほか、検査工程の増強に伴う人件費の問題も発生するでしょう。
一方、ポカヨケを導入しポカミスが起こりにくい状況をハード面から構築できれば、作業量のようなソフトパワーの増加に依存しない品質向上がなされます。
生産設備のなかには、作業ミスが重大な事故を招くものもあります。そのため、ポカヨケの導入は作業者の安全を確保し、労災を防止するという意味でも有効です。
たとえば、ボタンひとつで作動するプレス機の場合、ボタンに何かをぶつけてしまったり、うっかりボタンを押してしまったりした結果作動すると、労災事故につながりかねません。
そこで、ボタンを2つ押さないと稼動しないような仕組みを取り入れると、誤操作による事故の発生を防止できます。
製造現場においてポカミスが生じる理由の大半は、作業者自身が意図しないヒューマンエラーにあります。また、作業者の意図的行為(ルール違反)が介在する余地も指摘されています。
以下の観点からポカミスが起きる原因を理解し、適切なポカヨケ対策を講じることが、再発防止につながっていきます。
記憶エラーは、作業者が「覚えられない」「思い出せない」と、作業上の決まりごとを忘れてしまうことに起因するポカミスです。作業手順書やマニュアル、業務指示などを正確に記憶できず、誤った認識で作業に取り組むことは、いうまでもなくヒューマンエラーを招きます。
認知エラーは、作業者の見間違いや見逃し、聞き違いなどに起因するポカミスです。指示通達オペレーションや作業指示書への記載方法、あるいは材料の置き方などに問題があることが多いです。
判断エラーは、作業者が正しい判断ができないことに起因するポカミスです。生産設備や作業環境の問題が影響しているケースが多々あります。
行動エラーは、作業方法や作業手順を誤ることに起因するポカミスです。作業環境や教育の実施状況が行動エラーを誘発するケースが多いです。
ルール違反は、作業者が半ば意図的に手抜きをすることに起因するポカミスです。また、慣れによる油断が招くケースのほか、作業手順が複雑、あるいは業務量が多いケースなど、作業環境に関連していることもあります。
ヒューマンエラーを防ぐために、ポカヨケの仕組みづくりやその他の方法によってどのような対策が考えられるのか。具体的に次の7つの方法を取り上げていきます。
ポカミスの削減施策を立案するには、まずはミスの発生状況を整理し、ポカミスが起こる要因や、作業工程上の問題点を特定しなくてはいけません。
発生状況 | 問題点 |
---|---|
突発的にポカミスが発生する | 要因が顕在化せず、特定できていない |
同じ対策を講じても効果にばらつきがある | 同じ要因のミスとは限らず、原因を個別に特定できていない |
対策を行っても頻発する | 根本的な原因をつかみ、オペレーションを改善する必要がある |
対策を行った後、再び頻発する | 一定期間でミスが増加する要因を把握して、オペレーションを改善する必要がある |
イレギュラーな作業が多く、ミスが起こるケースが細分化している | イレギュラーな作業の指示方法などのオペレーションを改善する必要がある |
続いて、ポカミスが起こる要因ごとに、業務改善ポイントや具体的な原因を特定して対策を講じていきます。
ポカミスの発生は、作業環境やマニュアル・作業指示書、教育体制などの問題に関連しているケースが少なくありません。これらのポイントに応じて、対策を立てていく必要があります。
業務改善ポイント | 具体的な原因の例 |
---|---|
作業環境 |
|
マニュアル・作業指示書 |
|
教育体制 |
|
このように、業務改善ポイントを特定し、具体的な原因を排除してくための適切な措置を講じます。なお、業務内容を棚卸しして既存の課題を抽出するには、業務改善フレームワーク「ECRS」の活用も有効です。
また、具体的な原因によっては、そもそものヒューマンエラー対策として産業用ロボットの導入なども検討されるでしょう。
マニュアルがない、あるいはマニュアルがあっても作業フロー全体を網羅できていないケースなど、作業手順が曖昧化・属人化に陥る余地を残す現場では、ポカミスが頻発しがちです。
そもそも、作業者の解釈で異なる作業を行っていては、何を持ってミスとするのか、ポカミスの定義自体も曖昧になります。また、作業者による品質のバラツキが大きくなれば、全社レベルでの品質低下も危惧されるでしょう。
マニュアルの整備や教育体制の標準化は、ポカヨケ対策の大前提です。旧来の「背中を見て覚える」教育では、適切な技術伝承はなされません。作業の標準化、属人性の排除は、ポカミスの定義共有ならびに防止を促すほか、ルールにもとづいた作業意識も高まり、品質向上にも役立ちます。
加工や組立に使用する工具や治具の選定ミスは、作業指示に応じた適切な作業を阻害する要因となります。ポカミス対策として、誤った作業手順では使用できない機能を備えた治具もあるため、見直しも検討してみましょう。
また、適切な治具を導入していても、セットミスなどによるポカミスも起こりえます。治具や工具の置き場所の徹底、ラベリングなどの対策は必須です。
製造現場の5Sとは、「整理」「整頓」「清掃」「清潔」「しつけ」の5つの観点から、職場環境の改善・整備を実施する活動です。
作業場が整理整頓されておらず、部品や工具が散乱したような状況では、いうまでもなくポカミスが頻発します。想定外の事故を誘発するリスクも招きかねません。
5S活動の推進は、作業効率や生産性が向上するだけでなく、ポカミスの防止にも大いに役立ちます。
ポカミスの防止には、職場や作業中に潜む危険な現象を引き起こす危険要因に対する作業者自身の感受性を高め、解決していく能力を向上させるための訓練である、KYT(危険予知活動)の推進も効果的です。
KYTの進め方については、以下の記事で詳しく取り上げています。
ポカミスの発生要因として見逃せないのが、生産設備に関連する問題です。生産設備の不調に気づかず、無理な運用がなされているようなケースでは、誤動作などのヒューマンエラーをなくすことはできません。
また、生産設備の不具合も、ポカミスの発生と並んで不良品の生産や製造ラインのダウンタイムの長期化を招く要因になります。予防保全や予知保全による設備保全の徹底は欠かせません。
アラート設置などのポカヨケ対策を講じる際においても、設備保全に力を入れることは大前提になります。
トヨタ生産方式に由来するポカヨケは、不良品・欠品の発生防止や製造ラインのダウンタイム削減、労働災害の防止など、製造現場に多くのメリットを還元します。ヒューマンエラーを完全に防ぐことは極めて困難ではありますが、ミスの起きない仕組みづくりを怠っていては、生産性や品質の向上はなされないでしょう。
また、ポカヨケの仕組みや装置を導入した際には、設備保全の徹底による適切な運用も欠かせません。5S活動やKYTの実施も含め、ハード・ソフトの両面から適切なポカヨケ対策を講じましょう。
半導体・電池業界の研修実績年間10,000名を超える派遣会社が「今後の製造現場を左右する情報」をまとめた資料セットを作成しました。